Measuring progress
African Metrology and Testing Laboratory
Our services by commitment
News and Events
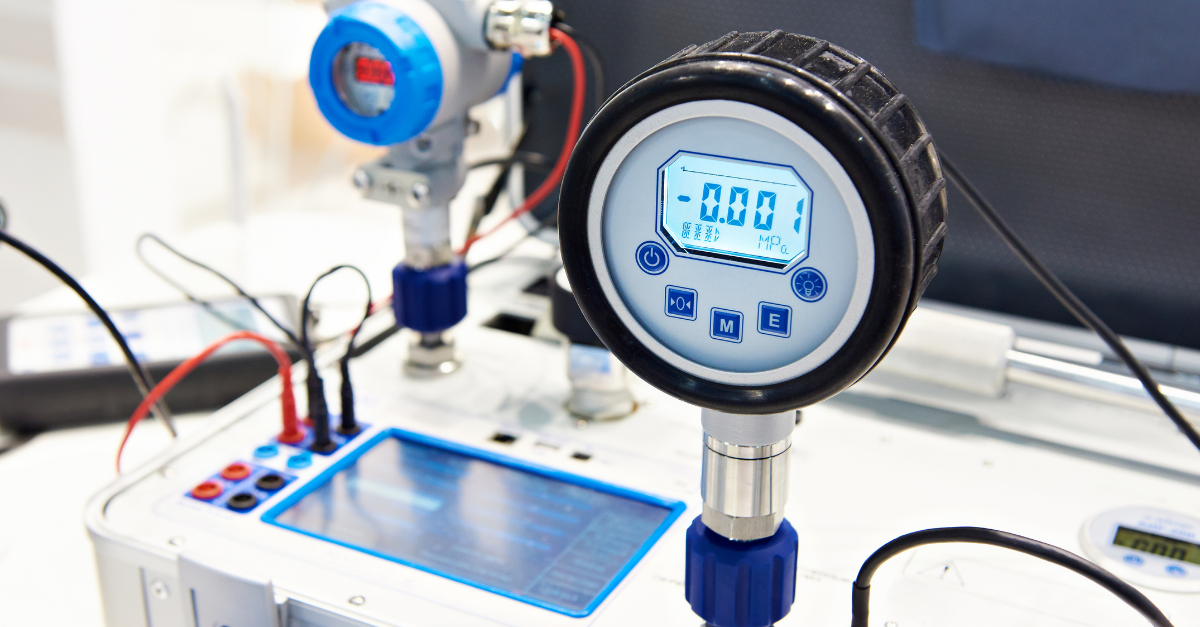
The Science of Measurement Understanding the Origins of Metrology The term metrology originates from ancient Greek, combining “metron” (measure) and “logos” (treatise or discourse). It is the science born from humanity’s need to quantify the world with precision, ensure the validity of those measurements, and establish their universal acceptance. A Fundamental Part of Everyday Life Measurement is deeply embedded in all aspects of human activity—scientific, industrial, and commercial. Each day, often without noticing, we rely on it in countless routine actions. Metrology plays a critical and growing role in key sectors such as: Energy and hydrocarbons Health and medical sciences Communications Agri-food and pharmaceutical industries Industrial safety and environmental protection The Importance of Accurate Measurements One of the oldest expectations from vendors is to give “honest weight and measure.” Whether it's a seller knowing exactly what they are offering or a buyer receiving exactly what they paid for, trust is built on accurate measurement. In today’s world of mass-produced, pre-packaged goods, accuracy remains just as essential—for instance, a 500g packet should contain 500g of product, no more, no less. A measurement—be it the weight of a bar of soap or the temperature at the outlet of a boiler—must be consistent and meaningful across time and place. This consistency is achieved through the regular calibration and verification of measuring instruments, ensuring they are aligned with international reference standards . This traceability makes the measurements reliable, valid, and universally recognized. The Birth of Modern Metrology Metrology, as a formal science, emerged in the 19th century during the industrial revolution. As global trade expanded, the need for standardized measurements became evident. The Metric System , initiated by a convention signed in Paris in 1840, laid the foundation for this unification. Today, the International System of Units (SI) serves as the global standard, ensuring all measurements are traceable to universally accepted references. Measurement: A Pillar of Industrial Quality In industrial settings, production processes rely heavily on instruments that measure pressure, temperature, weight, flow rate, and dimensions. The accuracy of these instruments directly influences: Product and service quality Operational safety Risk management Environmental compliance In high-stakes sectors such as pharmaceuticals, agri-food, and petrochemicals, controlling measurement instruments is not optional—it’s a regulatory necessity. These tools must be accurately maintained and monitored to stay within acceptable error margins. Global Compliance and Market Access Regional harmonization of laws (e.g., in the EU) and the growth of international standards have introduced new technical requirements. Major markets—such as the European Economic Area (EEA)—are now protected by non-tariff barriers that enforce strict product and quality standards. Among these are metrological requirements. To gain market access, businesses must prove that their measuring instruments are compliant and traceable to SI standards maintained by the BIPM (International Bureau of Weights and Measures) . Standards That Demand Metrological Rigor International standards like ISO 9001 (quality management) , ISO 14001 (environmental management) , and those related to industrial safety require organizations to control and calibrate their measuring devices. The objective evidence of quality depends on measurement—and trustworthy measurements require ongoing verification and traceability. Internal and External Impacts of Measurement Control For a business, controlling measurement tools is crucial for both internal efficiency and external credibility. Internally : To optimize production processes To ensure worker and equipment safety To limit environmental impact Externally : To pass audits for certifications To qualify for international tenders and markets To demonstrate conformity with industry regulations Calibration: The Backbone of Reliable Measurement Mastery over measuring instruments comes from regular calibration and verification . These processes link a measurement back to international standards, ensuring it is universally recognized, consistent, and meaningful. A Regional Challenge and Opportunity The challenge was clear: To design, document, implement, and manage the first scientific and technical metrology laboratory in the UEMOA region —a laboratory tailored to the needs of industry and fully compliant with international norms.
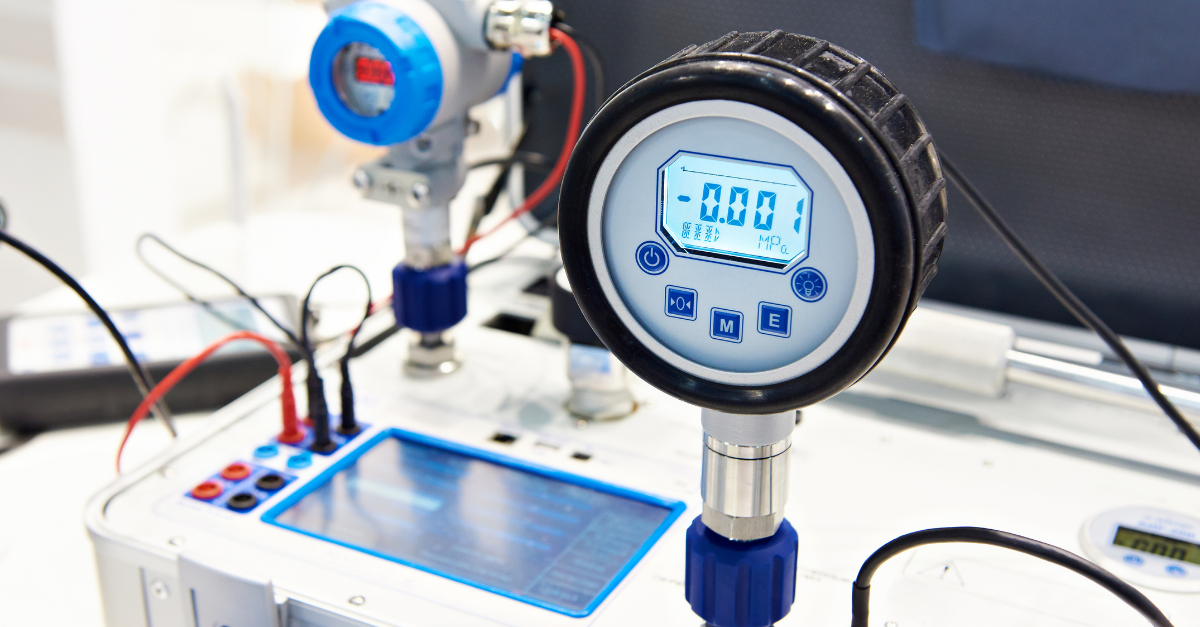
The Science of Measurement Understanding the Origins of Metrology The term metrology originates from ancient Greek, combining “metron” (measure) and “logos” (treatise or discourse). It is the science born from humanity’s need to quantify the world with precision, ensure the validity of those measurements, and establish their universal acceptance. A Fundamental Part of Everyday Life Measurement is deeply embedded in all aspects of human activity—scientific, industrial, and commercial. Each day, often without noticing, we rely on it in countless routine actions. Metrology plays a critical and growing role in key sectors such as: Energy and hydrocarbons Health and medical sciences Communications Agri-food and pharmaceutical industries Industrial safety and environmental protection The Importance of Accurate Measurements One of the oldest expectations from vendors is to give “honest weight and measure.” Whether it's a seller knowing exactly what they are offering or a buyer receiving exactly what they paid for, trust is built on accurate measurement. In today’s world of mass-produced, pre-packaged goods, accuracy remains just as essential—for instance, a 500g packet should contain 500g of product, no more, no less. A measurement—be it the weight of a bar of soap or the temperature at the outlet of a boiler—must be consistent and meaningful across time and place. This consistency is achieved through the regular calibration and verification of measuring instruments, ensuring they are aligned with international reference standards . This traceability makes the measurements reliable, valid, and universally recognized. The Birth of Modern Metrology Metrology, as a formal science, emerged in the 19th century during the industrial revolution. As global trade expanded, the need for standardized measurements became evident. The Metric System , initiated by a convention signed in Paris in 1840, laid the foundation for this unification. Today, the International System of Units (SI) serves as the global standard, ensuring all measurements are traceable to universally accepted references. Measurement: A Pillar of Industrial Quality In industrial settings, production processes rely heavily on instruments that measure pressure, temperature, weight, flow rate, and dimensions. The accuracy of these instruments directly influences: Product and service quality Operational safety Risk management Environmental compliance In high-stakes sectors such as pharmaceuticals, agri-food, and petrochemicals, controlling measurement instruments is not optional—it’s a regulatory necessity. These tools must be accurately maintained and monitored to stay within acceptable error margins. Global Compliance and Market Access Regional harmonization of laws (e.g., in the EU) and the growth of international standards have introduced new technical requirements. Major markets—such as the European Economic Area (EEA)—are now protected by non-tariff barriers that enforce strict product and quality standards. Among these are metrological requirements. To gain market access, businesses must prove that their measuring instruments are compliant and traceable to SI standards maintained by the BIPM (International Bureau of Weights and Measures) . Standards That Demand Metrological Rigor International standards like ISO 9001 (quality management) , ISO 14001 (environmental management) , and those related to industrial safety require organizations to control and calibrate their measuring devices. The objective evidence of quality depends on measurement—and trustworthy measurements require ongoing verification and traceability. Internal and External Impacts of Measurement Control For a business, controlling measurement tools is crucial for both internal efficiency and external credibility. Internally : To optimize production processes To ensure worker and equipment safety To limit environmental impact Externally : To pass audits for certifications To qualify for international tenders and markets To demonstrate conformity with industry regulations Calibration: The Backbone of Reliable Measurement Mastery over measuring instruments comes from regular calibration and verification . These processes link a measurement back to international standards, ensuring it is universally recognized, consistent, and meaningful. A Regional Challenge and Opportunity The challenge was clear: To design, document, implement, and manage the first scientific and technical metrology laboratory in the UEMOA region —a laboratory tailored to the needs of industry and fully compliant with international norms.
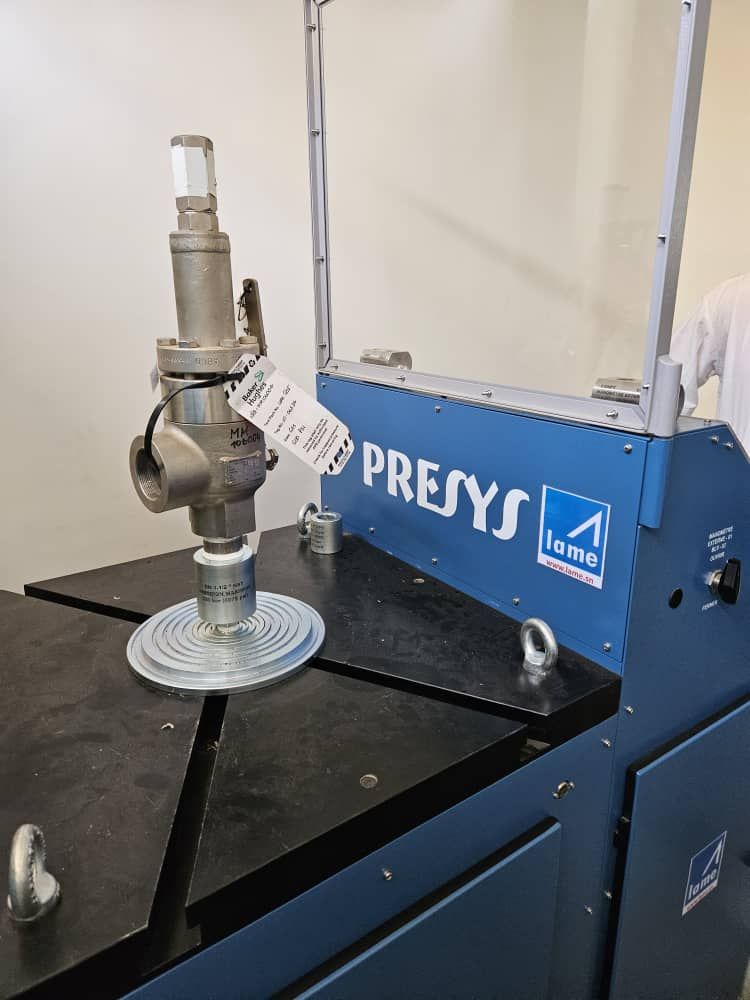
Safety valves are critical components in any pressurized system — boilers, compressors, tanks, or industrial installations. Their purpose? To release excess pressure and prevent any risk of explosion or material damage. But to fulfill this role effectively, they must be accurately calibrated , meaning adjusted to open at the exact pressure defined by the manufacturer or relevant standards (API, ASME, etc.). Purpose of Pressure Calibration: Identify the valve (reference, pressure range, type of fluid, use). Note the set pressure. Isolate the valve from the system if fitted. Ensure that the test devices are calibrated themselves (ISO 17025 traceability). Pressure Calibration Methodology 1. Valve Preparation Identify the valve (reference, pressure range, fluid type, usage). Record the set pressure (Set Pressure). Isolate the valve from the system if it is already installed. Ensure that all testing devices are themselves calibrated (ISO 17025 traceability). 2. As Found Test (Before Adjustment) Mount the valve on a pressure test bench (hydraulic or pneumatic). Apply pressure gradually. Read the actual opening pressure (Pop pressure). Note any deviations from the set point. This test indicates whether the valve has drifted and whether readjustment is necessary. 3. Mechanical Adjustment (Tuning) If the valve does not open at the correct pressure: Remove the cover Adjust the spring tension or adjust the disc according to the design. Carry out several tests until the target opening pressure is reached.. 4. Pop Test Perform a dynamic aperture test, observing : The "pop" noise (sudden release). Exact release pressure. The responsiveness of the mechanism. Make sure the valve closes properly after release. 5. Leak Test (Bubble Test) Use a visual method (foam solution or immersion) to: Check valve tightness below the set pressure. Detect any premature leakage. 6. As Left Test (Post-Calibration) Record the final opening pressure after adjustment. Ensure compliance within acceptable tolerance (typically ±3% of the set point). Issue a calibration certificate including: Before/after results. Test conditions. Equipment used. Traceability references. Equipment Used Pressure test bench (air or water). Precision manometer or digital sensor (calibrated). Manual or automatic pumps. Cameras or sensors for bubble testing (tightness). Calibration management software.